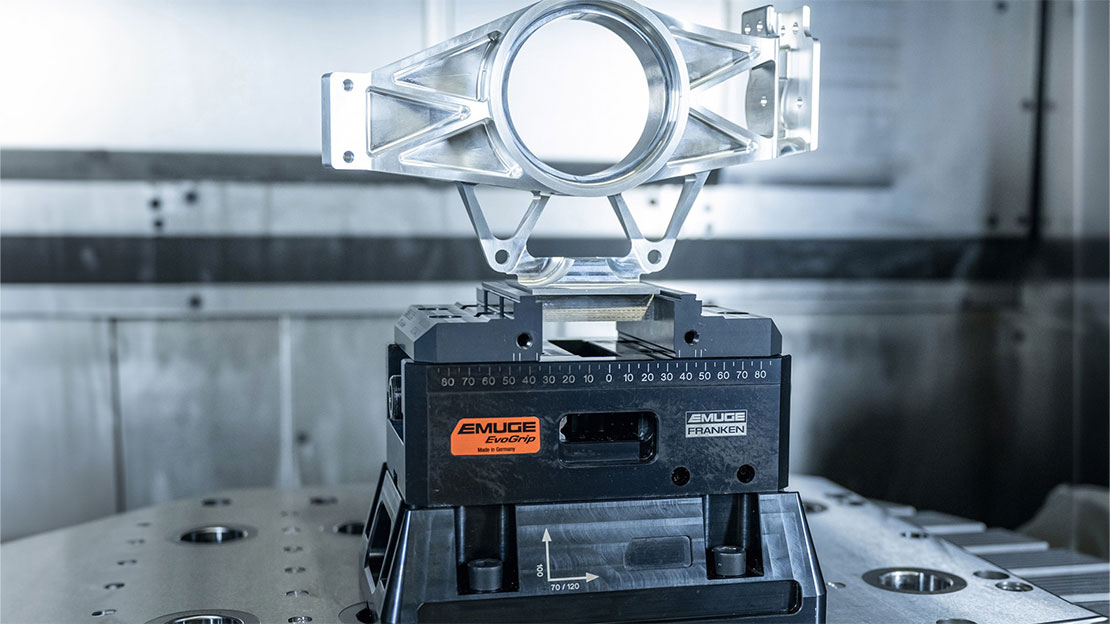
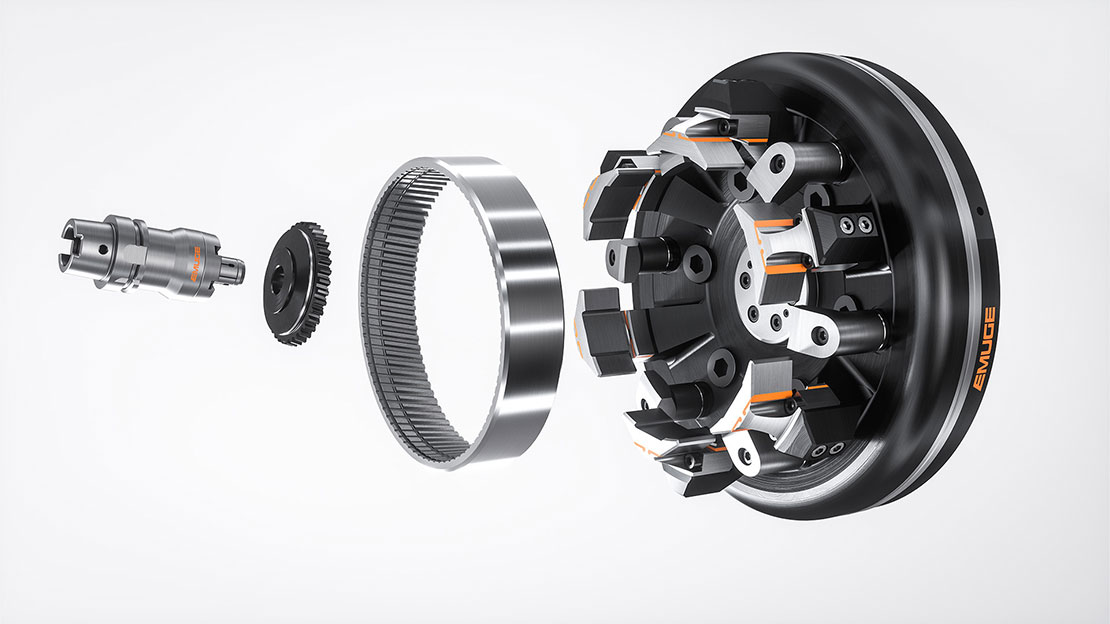
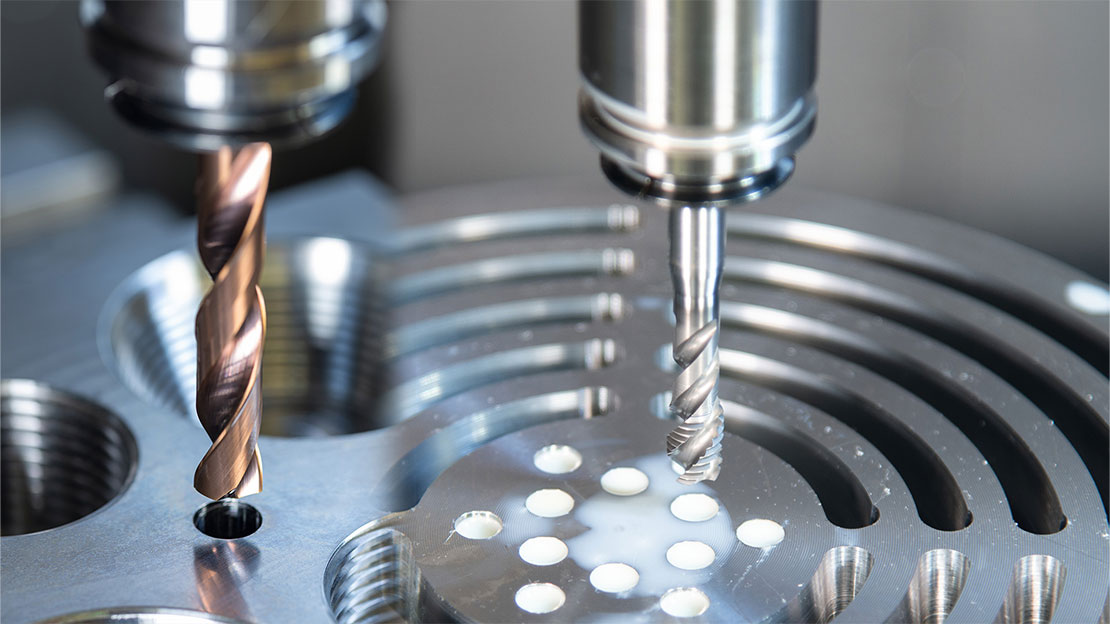
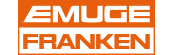
- EMUGE-Werk Richard Glimpel GmbH & Co. KG
- Nürnberger Straße 96 - 100
DE-91207 Lauf - https://www.emuge-franken.com
Exhibitor description
EMUGE-FRANKEN, the comprehensive provider of precision tools and efficient machining processes,
is closely connected to its customers, offering precision, a wide range of capabilities, and operating in 53 countries worldwide. With a diverse portfolio for drilling, threading, clamping, testing, and milling, the family-owned EMUGE-FRANKEN group has been a leading provider for over 100 years.
With around 1,900 employees dedicated to developing, manufacturing, and distributing innovative tool solutions, EMUGE-FRANKEN offers a product range of 40,000 stocked items along with numerous custom-made products, focusing on applications in the automotive, power plant, aerospace, medical technology, machinery, and plant engineering industries. These tools enable highly efficient machining in serial production, boasting impressive tool life even when processing new, challenging materials.
Under the "Dental" product line, FRANKEN provides tools such as cutters, grinding pins, and twist drills for dental professionals to create dental prosthetics. The extensive service offering supports the entire machining system chain, including not only machining tools but also coordinated tool holders or customized workpiece clamping devices. All activities aim to optimize manufacturing processes in machining, providing customers with new solutions to save time and costs.
We are delighted to present our product highlights for the year 2025:
1. Empowering new standard workholding solutions with the EvoGrip Centric Clamping Systems!
This new combination enhances productivity in workpiece clamping, especially in the 5-axis machining of raw parts and more! While EMUGE has traditionally been associated with custom solutions for specific applications in workholding technology, now you can achieve maximum efficiency with standard workholding solutions.
More than just a vise: EvoGrip Centric Clamping Systems are manually operated direct clamps that center the workpiece. The compact design allows for multi-sided machining of fixed workpieces across five axes (5-axis machining). With a modular, slim system design and clamping force of up to 75 kN, these centric clamps enable secure milling of complex, overhanging workpieces. Various jaw configurations allow for versatile clamping setups.
Comprehensive workholding solutions: With the EvoGrip Centric Clamping Systems, EMUGE complements its established clamping systems, enhancing flexibility in machining. Explore the new possibilities of workpiece clamping for your components!
2. The complete solution for SKIVING: Tools and clamping devices for hobbing from a single source!
Modern hobbing enables the production of gearings (external and internal gears), whether straight or helical. Hobbing is highly productive, provided that the machine, tool, and workpiece are perfectly aligned. Skiving offers an economical alternative to manufacturing processes such as hobbing and broaching. In addition to workpiece clamping, tool clamping and hobbing tools are supplied from a single source. Each skiving tool from FRANKEN is individually tailored to customer needs. FRANKEN also provides cutting strategies and cutting parameters optimized for specific applications. EMUGE membrane chucking systems have been used for precise workpiece clamping for many years.
3. Drilling and tapping in stainless steel: New twist drills and machine taps for stainless steel!
You're familiar with the challenges of drilling holes and tapping threads in stainless steel, which still require precise tools, skilled operators, and careful processes. With the EMUGE InoxDrill twist drill and the Enorm Inox tap, along with EMUGE-recommended machining parameters, you can increase process reliability and reduce production costs. The adhesion tendency of stainless steel is reduced in the InoxDrill twist drill through special topography and macrogeometry. The coordinated interplay of geometry, cutting data, and coating enables impressive tool life. Unlike drilling, there's no geometric way to induce chip breakage when creating threads in stainless steel. The solution lies in defined chip formation through the geometry of the tap. To minimize machine stops for chip removal, reducing chip jamming is also crucial.